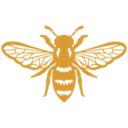
Admin at Alvacus
Beam Bending Stress formula calculator
Description
This online beam bending stress calculator helps you analyze and design beams with accuracy and efficiency. Calculate stress, identify critical sections, and ensure structural integrity. Quickly solve for bending moments, shear forces, and maximum bending stress. Supports various beam types and loading conditions. Get started for free!
Info
Table of Contents
- Introduction
- Understanding the Beam Bending Stress Formula
- Applying the Beam Bending Stress Formula
- Cantilever Beam Bending Stress
- How to Calculate Maximum Bending Stress in a Beam: Example Calculations for Different Beam Geometries
- FAQs
- Conclusion and Final Thoughts
- Glossary of terms
- Useful calculators
Introduction
What is Beam Bending Stress?
Beam bending stress arises when a beam experiences a force that causes it to bend. This internal force, also known as a bending moment, creates tension and compression on opposite sides of the beam's cross-section. Understanding the magnitude and distribution of this stress is crucial in ensuring the safety and functionality of beams in various structures.
The Importance of Understanding Beam Bending Stress
The ability to calculate beam bending stress helps engineers design and analyze a wide range of structures, from simple beams in buildings to complex components in airplanes and bridges. Understanding the stress distribution within a beam allows engineers to:
- Ensure the beam's strength: By comparing the calculated bending stress with the material's yield strength, engineers can verify if the beam can withstand the applied loads without exceeding its elastic limit.
- Optimize beam design: By analyzing the stress distribution across different cross-sectional shapes, engineers can optimize the design of the beam for efficiency and material usage.
- Prevent premature failure: By identifying areas of high stress concentration, engineers can implement preventative measures like adding reinforcements or modifying the geometry to mitigate the risk of failure.
Applications of the Beam Bending Stress Formula
The beam bending stress formula has numerous applications across various engineering disciplines, including:
- Civil engineering: Designing beams in buildings, bridges, and other structures.
- Mechanical engineering: Analyzing components in machines, vehicles, and aircraft.
- Aerospace engineering: Designing wings and other structural elements in airplanes.
- Biomechanical engineering: Analyzing bones and other tissues in the human body.
By mastering the beam bending stress formula and its applications, you'll be equipped with a fundamental tool for tackling diverse engineering challenges.
Understanding the Beam Bending Stress Formula
Variables and Definitions:
The beam bending stress formula is represented as:
σ = M * c / I
where:
- σ is the bending stress (units: Pa or psi)
- M is the bending moment (units: N-m or lb-ft)
- c is the distance from the neutral axis to the point where the stress is calculated (units: m or ft)
- I is the moment of inertia of the beam's cross-section (units: m^4 or ft^4)
Formula Breakdown:
- Moment of Inertia (I):
-
The moment of inertia for a rectangular cross-section (II) is calculated as:
I = (b * h^3) / 12
This represents the distribution of the cross-sectional area with respect to an axis.
- Bending Stress (σ):
-
The bending stress (σσ) in the beam is determined by:
σ = (M * c) / I
It quantifies the internal stresses induced by the bending moment.
Combined Formula:
-
Substitute the expression for II into the bending stress formula:
Simplify to:
σ = (12 * M * c) / (b * h^3)
Applying the Beam Bending Stress Formula
Identifying Bending Moments and Shear Forces:
The first step in applying the beam bending stress formula is to determine the bending moment and shear force acting on the beam. These values can be obtained through various methods, depending on the specific loading and support conditions. Common methods include:
- Free body diagrams: Drawing and analyzing forces acting on the beam and its supports.
- Equilibrium equations: Applying Newton's laws to solve for unknown forces and moments.
- Moment distribution method: A numerical technique for analyzing statically indeterminate beams.
Determining the Moment of Inertia for Various Beam Cross-Sections:
The moment of inertia is a geometric property that quantifies the resistance of a cross-section to bending. Different shapes have different moment of inertia values, which can be found from standard tables or calculated using specific formulas.
Calculating Maximum Bending Stress:
Once you have determined the bending moment and moment of inertia, you can calculate the maximum bending stress by utilizing the formula:
σ_max = M_max * c_max / I
where:
- σ_max is the maximum bending stress
- M_max is the maximum bending moment
- c_max is the maximum distance from the neutral axis to the outermost fiber of the cross-section
By identifying the critical section of the beam (where the maximum bending moment occurs), you can accurately assess the potential for failure.
Cantilever Beam Bending Stress
Cantilever beams are beams fixed at one end and free at the other. They are commonly used in various structures like balconies, overhangs, and diving boards. Analyzing the bending stress in these beams requires specific considerations:
Calculating Bending Moment and Shear Force for Cantilever Beams:
For a cantilever beam subjected to a concentrated load at the free end, the bending moment varies linearly from zero at the fixed end to a maximum at the free end. The shear force remains constant throughout the beam and is equal to the applied load.
Applying the Beam Bending Stress Formula to Cantilever Beams:
The maximum bending stress in a cantilever beam occurs at the fixed end, where the bending moment is the greatest. You can calculate it using the formula:
σ_max = (P * L) / I
where:
- P is the applied load
- L is the length of the beam
This simplified formula is specific to cantilever beams with concentrated loads at the free end. For more complex loading scenarios, the bending moment distribution along the beam needs to be considered.
How to Calculate Maximum Bending Stress in a Beam: Example Calculations for Different Beam Geometries
This section delves into practical applications of the beam bending stress formula by showcasing example calculations for different beam geometries under various loading conditions.
Example 1: Simply Supported Beam with Point Load
Beam Properties:
- Material: Steel
- Yield Strength: 250 MPa
- Cross-section: Rectangular (b = 50mm, h = 100mm)
- Length: 2 m
- Point load: 10 kN applied at mid-span
Solution:
- Calculate the moment of inertia:
I = bh^3 / 12 = (50mm * 100mm^3) / 12 = 416,666.67 mm^4
- Determine the maximum bending moment:
M_max = P * L / 4 = 10 kN * 2 m / 4 = 5 kNm
- Identify the critical section:
The critical section is located at the mid-span.
- Calculate the maximum bending stress:
σ_max = M_max * c_max / I = 5 kNm * 50mm / 416,666.67 mm^4 = 59.53 MPa
Interpretation:
The calculated maximum bending stress of 59.53 MPa is well below the yield strength of steel (250 MPa). Therefore, the beam is safe from yielding under the applied load.
Example 2: Cantilever Beam with Uniform Load
Beam Properties:
- Material: Aluminum
- Yield Strength: 150 MPa
- Cross-section: Circular (diameter = 50mm)
- Length: 1 m
- Uniform load: 5 kN/m
Solution:
- Calculate the moment of inertia:
I = π * (d^4) / 64 = π * (50mm)^4 / 64 = 31,415.93 mm^4
- Determine the maximum bending moment:
M_max = w * L^2 / 2 = 5 kN/m * (1 m)^2 / 2 = 2.5 kNm
- Identify the critical section:
The critical section is located at the fixed end.
- Calculate the maximum bending stress:
σ_max = M_max * c_max / I = 2.5 kNm * 25mm / 31,415.93 mm^4 = 19.74 MPa
Interpretation:
The calculated maximum bending stress of 19.74 MPa is significantly lower than the yield strength of aluminum (150 MPa). The beam is safe from yielding under the uniform load.
These examples illustrate how to apply the beam bending stress formula to different scenarios. By modifying the beam properties, loading conditions, and cross-sectional shapes, you can analyze diverse beam configurations and ensure their structural integrity.
Frequently Asked Questions (FAQ)
Q1: What are the factors that affect beam bending stress?
Several factors influence the bending stress in a beam, including:
- Material properties: The yield strength and modulus of elasticity of the material directly affect the maximum stress the beam can withstand.
- Cross-sectional shape: The geometry of the cross-section significantly impacts the moment of inertia, which in turn influences the stress distribution within the beam.
- Applied loads: The magnitude, location, and type of loading (point load, distributed load, etc.) determine the bending moment distribution along the beam.
- Beam geometry: The length, cross-sectional dimensions, and support conditions influence the behavior of the beam under load.
Q2: How does the cross-sectional shape of a beam affect its bending stress?
The cross-sectional shape plays a crucial role in resisting bending. Shapes with larger moment of inertia, like rectangular sections with larger width and height, can withstand higher bending loads compared to shapes with smaller moment of inertia, like circular sections. Additionally, shapes with more material concentrated further away from the neutral axis offer greater bending resistance.
Q3: What is the difference between bending stress and shear stress?
While both are internal forces acting within a beam, they differ in their nature and direction:
- Bending stress: Caused by the bending moment, it creates tension on one side of the beam and compression on the opposite side. This stress acts perpendicular to the cross-section.
- Shear stress: Caused by the shear force, it acts parallel to the cross-section, tending to slide one section of the beam past another.
Q4: What are the limitations of the beam bending stress formula?
The beam bending stress formula assumes several idealizations, including:
- Linear-elastic behavior of the material
- Pure bending without shear forces
- Uniform and isotropic material properties
- Homogeneous cross-section along the beam length
In real-world scenarios, these assumptions may not always hold true. Therefore, it's important to understand the limitations and consider potential deviations for more complex situations.
Q5: What are some alternative methods for analyzing beam bending stress?
Besides the beam bending stress formula, other methods can be used to analyze beam behavior:
- Moment-area method: Provides a graphical approach to determine slopes and deflections in beams.
- Conjugate beam method: Utilizes a fictitious beam to simplify the analysis of real beams with complex loading conditions.
- Finite element analysis: A computational method that divides the beam into small elements and analyzes their interaction under load, offering a highly accurate solution for complex geometries and loading scenarios.
These methods offer valuable tools for advanced analysis of beams and can be used in conjunction with the beam bending stress formula for a comprehensive understanding of beam behavior.
Conclusion
The beam bending stress formula is a fundamental tool for engineers and anyone involved in analyzing and designing structures. By understanding the formula's derivation, application, and limitations, you can assess the behavior of beams under various loading conditions and ensure their safety and functionality. Remember to:
- Verify your calculations: Double-check your calculations for accuracy and ensure they are consistent with realistic material properties and design specifications.
- Utilize additional resources: Refer to engineering textbooks, online tutorials, and design codes for further guidance and deeper understanding of beam bending concepts.
- Incorporate additional considerations: Explore advanced topics like stress concentration, fatigue loading, and buckling to gain a holistic view of beam behavior under diverse conditions.
By mastering the beam bending stress formula and applying it with critical thinking and comprehensive knowledge, you can contribute to the design and construction of safe and efficient structures.
Glossary of Terms
Bending Moment: An internal force that causes a beam to bend. It is measured in units of N-m or lb-ft.
Moment of Inertia: A geometric property that quantifies the resistance of a cross-section to bending. It is measured in units of m^4 or ft^4.
Neutral Axis: The imaginary line within a beam's cross-section that experiences no stress due to bending.
Section Modulus: A geometric property related to the moment of inertia and the distance from the neutral axis to the outermost fiber of the cross-section. It is used to calculate bending stress for specific shapes.
Yield Strength: The maximum stress a material can withstand before undergoing permanent deformation. It is measured in units of Pa or psi.
Ultimate Strength: The maximum stress a material can withstand before failing completely. It is measured in units of Pa or psi.
Stress Concentration: A localized increase in stress around geometric discontinuities like holes, notches, or sharp corners.
Factor of Safety: A design parameter used to ensure the safety of a structure by accounting for uncertainties in load, material properties, and analysis methods.
References
- Hibbeler, R. C. (2011). Mechanics of Materials (8th ed.). Prentice Hall.
- Beer, F. P., Johnston, E. R., DeWolf, J. T., & Mazurek, D. F. (2019). Mechanics of Materials (7th ed.). McGraw-Hill Education.
- Gere, J. M., & Goodno, B. J. (2013). Mechanics of Materials (8th ed.). Cengage Learning.
- American Institute of Steel Construction (AISC). (2017). Manual of Steel Construction: Load and Resistance Factor Design (15th ed.). AISC.
- American Society of Civil Engineers (ASCE). (2010). Minimum Design Loads for Buildings and Other Structures (ASCE/SEI 7-10). ASCE.
Useful calculators
To further enhance your knowledge, check out these calculators and resources:
- Pascal (Pa) to standard atmosphere (atm) converter
- The Darcy-Weisbach equation formula calculator
- Pascal to pounds per square inch (psi) converter
By exploring these resources, you can broaden your understanding of various concepts.