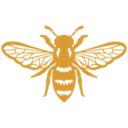
Admin at Alvacus
Economic Order Quantity (EOQ) formula calculator
Description
Unleash Inventory Efficiency with Our EOQ Calculator. Discover the ideal order quantity to minimize costs and maximize profits with our user-friendly Economic Order Quantity (EOQ) calculator. Streamline inventory management and boost supply chain efficiency today.
Info
Table of Contents
- Introduction
- Economic Order Quantity Formula
- Importance of Economic Order Quantity Model
- Balancing Costs with EOQ
- FAQs
- Conclusion
- Useful calculators
Introduction
What is Economic Order Quantity?
Economic Order Quantity (EOQ) is a formula used in inventory management to determine the optimal quantity of items a business should order to minimize carrying costs and ordering costs. The EOQ formula takes into account the carrying cost of holding inventory, the ordering cost of purchasing inventory, and the demand rate of the inventory item. By calculating the EOQ, a business can determine the most cost-effective method for ordering and holding inventory. This formula helps businesses make informed decisions that can increase profitability. Do you want to know more about the advantages and disadvantages of using EOQ or other inventory management formulas? Let's dive deeper!
The Objective of Economic Order Quantity
The objective of Economic Order Quantity (EOQ) is to determine the ideal order size in units or quantities of materials to avoid stockouts and overstocking, while minimizing carrying costs1 2. By calculating the EOQ, businesses can strike a balance between ordering costs and holding costs, ensuring the efficient management of inventory1. This not only helps prevent shortages that can lead to customer dissatisfaction but also reduces the expenses associated with excess inventory2. By optimizing the order quantity, businesses can enhance operational efficiency and maximize profitability.
Sources:
-
Investopedia - Economic Order Quantity: What Does It Mean and Who Is It
-
MRPeasy - What Is Economic Order Quantity (EOQ) and the EOQ Formula?
Economic Order Quantity Formula
The Economic Order Quantity (EOQ) formula is calculated using the following steps:
Step 1: Gather Information
- Demand (D): Determine the annual demand for the product. For example, let's say the annual demand for a particular product is 10,000 units.
- Ordering Cost per Order (S): Identify the cost of placing an order. If each order costs $200, this is your ordering cost per order.
- Holding Cost per Unit (H): Determine the cost to hold one unit in inventory for a year. If the holding cost per unit is $2, this is your holding cost.
Step 2: Plug Values into the Formula
The EOQ formula is:
EOQ = √2DS/H
Step 3: Calculate EOQ
Using our example:
EOQ = √(2 * 10000 * 200) / 2
EOQ = √(4000000) / 2
EOQ = √2000000
EOQ ≈ 1414.21
Step 4: Interpret the Result
The calculated EOQ is approximately 1414.21 units
How to Calculate Economic Order Quantity
Now that we have the EOQ (1414.21 units), you can use this quantity as the optimal order size to minimize total inventory costs. This means that ordering this quantity will balance the costs of ordering and holding inventory, leading to the most cost-effective inventory management.
Examples of Economic Order Quantity Calculation
To further illustrate, let's consider two scenarios:
Scenario 1: Ordering 1414 Units
- Number of Orders: 10000 / 1414 ≈ 7.07
- Total Ordering Cost: 7.07 * 200 = 1414
- Total Holding Cost: (1414.21 / 2) * 2 ≈ 1414.21
- Total Cost: 1414 + 1414.21 ≈ 2828.21
Scenario 2: Ordering 1000 Units
- Number of Orders: 10000 / 1000 = 10
- Total Ordering Cost: 10 * 200 = 2000
- Total Holding Cost: (1000 / 2) * 2 = 1000
- Total Cost: 2000 + 1000 = 3000
In this example, ordering 1414 units results in a lower total cost compared to ordering 1000 units, demonstrating the cost-saving benefits of using the EOQ.
Understanding and applying the EOQ formula is essential for businesses to optimize their inventory management processes and reduce overall costs.
Importance of Economic Order Quantity Model
In the bustling world of business, inventory management often resembles a delicate dance, a balancing act between minimizing costs and maintaining adequate stock levels1. Amidst this intricate choreography, the Economic Order Quantity (EOQ) model emerges as a beacon of guidance, illuminating the path towards optimal inventory control.
Imagine a business grappling with the dilemma of ordering inventory: too little, and stockouts lead to lost sales and disgruntled customers; too much, and storage costs skyrocket, eroding profitability. The EOQ model steps in, wielding the power of mathematical precision to determine the ideal order quantity, that sweet spot where costs and customer satisfaction converge.
At its core, the EOQ model is a cost optimization tool, meticulously balancing the opposing forces of inventory holding costs and ordering costs2. Inventory holding costs, those associated with storing and maintaining stock, include expenses such as rent, utilities, and insurance3. Ordering costs, on the other hand, encompass the expenses incurred with each order, such as processing fees, shipping charges, and potential discounts for larger orders.
By striking a harmonious balance between these competing cost factors, the EOQ model unlocks a realm of benefits, transforming inventory management from a chaotic juggling act into a symphony of efficiency. Reduced stockouts, streamlined ordering processes, and optimized storage space are just a few of the melodies that resonate from this powerful tool.
In the hands of savvy business owners, the EOQ model becomes a strategic weapon, empowering them to navigate the inventory maze with precision and finesse. By harnessing its power, businesses can bid farewell to the days of inventory woes and embrace a future of optimized costs, enhanced customer satisfaction, and a resounding chorus of success.
Sources:
-
TVSSCS - The Importance of Inventory Management in Your Supply Chain
-
Investopedia - How Is the Economic Order Quantity Model Used in Inventory Management?
Balancing Costs with EOQ: Striking the Right Chord
The Economic Order Quantity (EOQ) model is a cornerstone of inventory management, helping businesses optimize the balance between ordering costs and holding costs1. Striking this equilibrium is crucial for maintaining profitability and ensuring customer satisfaction.
Minimizing Inventory Holding Costs
Inventory holding costs encompass the expenses associated with storing and maintaining stock2. These costs include rent, utilities, insurance, depreciation, obsolescence, and potential losses due to damage or theft.
Reducing Ordering Costs
Ordering costs represent the expenses incurred with each order placement3. These costs include order processing fees, shipping charges, and potential discounts for larger orders.
The EOQ Dance
The EOQ model plays a critical role in balancing these opposing cost factors4. By identifying the order quantity that minimizes the total cost of inventory, businesses can achieve significant savings and enhance their overall efficiency5.
Sources:
-
ScienceDirect - The economic order quantity model with compounding
-
Investopedia - What Are Holding Costs? Definition, How They Work, and Example
-
Shiphero - What are Ordering Costs? Understanding the Fundamentals
-
Linkedin - Optimizing Inventory Management: Leveraging the Theory of Economic Order Quantity
-
CFBLOG - Maximizing Efficiency: Understanding the Economic Order Quantity Model
Frequently Asked Questions (FAQ)
Q1: How does Economic Order Quantity minimize total costs?
Economic Order Quantity (EOQ) minimizes total costs by balancing the trade-off between ordering costs and holding costs. Ordering costs are the expenses incurred each time an order is placed, such as processing fees, shipping charges, and potential discounts for larger orders. Holding costs are the expenses associated with storing and maintaining inventory, such as rent, utilities, insurance, depreciation, obsolescence, and potential losses due to damage or theft.
The EOQ formula identifies the order quantity that minimizes the sum of these two costs. By maintaining inventory levels at the EOQ, businesses can achieve significant savings and enhance their overall efficiency.
Q2: What is the role of the EOQ formula in inventory management?
The EOQ formula plays a crucial role in inventory management by providing a mathematical framework for determining the optimal order quantity. This framework helps businesses strike a balance between ordering costs and holding costs, leading to reduced inventory costs, improved customer satisfaction, and enhanced profitability.
Q3: Can Economic Order Quantity be applied to different industries?
Yes, the EOQ model can be applied to a wide range of industries, including manufacturing, retail, healthcare, and distribution. The basic principles of the EOQ model remain consistent across industries, but the specific parameters, such as demand, holding costs, and ordering costs, may vary depending on the industry and the specific product or service being inventoried.
Q4: Are there any limitations to the EOQ model?
While the EOQ model is a valuable tool for inventory management, it is important to recognize its limitations. The EOQ model assumes that demand is constant and known with certainty, which is not always the case. Additionally, the EOQ model does not consider factors such as lead times, safety stock, or discounts for larger orders.
Q5: How frequently should EOQ be recalculated?
The frequency with which EOQ should be recalculated depends on the specific circumstances of the business. However, it is generally recommended to recalculate EOQ whenever there is a significant change in demand, holding costs, or ordering costs.
Q6: What factors influence the determination of Economic Order Quantity?
The determination of Economic Order Quantity (EOQ) is influenced by several factors, including:
- Annual demand: The total amount of a product or item that a business expects to sell in a year.
- Holding cost per unit per year: The cost associated with storing and maintaining one unit of inventory for one year. This includes expenses such as rent, utilities, insurance, depreciation, obsolescence, and potential losses due to damage or theft.
- Ordering cost per order: The fixed cost incurred each time an order is placed, regardless of the order quantity. This includes expenses such as processing fees, shipping charges, and potential discounts for larger orders.
Q7: Is Economic Order Quantity applicable to both large and small businesses?
Yes, Economic Order Quantity (EOQ) is applicable to both large and small businesses. However, the specific implementation of EOQ may vary depending on the size and resources of the business.
- Large businesses: Large businesses with sophisticated inventory management systems and access to detailed data can use the EOQ formula directly to calculate the optimal order quantity.
- Small businesses: Small businesses with limited resources or data availability may need to simplify the EOQ formula or use alternative methods to estimate the optimal order quantity.
Q8: How does EOQ contribute to supply chain optimization?
Economic Order Quantity (EOQ) contributes to supply chain optimization in several ways, including:
- Reduced inventory costs: EOQ helps businesses minimize the total cost of inventory by balancing ordering costs and holding costs. This can lead to significant savings and improved profitability.
- Improved inventory turnover: EOQ helps businesses maintain the right level of inventory to meet customer demand without overstocking. This can lead to faster inventory turnover and a more efficient supply chain.
- Enhanced customer service levels: By reducing stockouts and ensuring prompt order fulfillment, EOQ can help businesses improve customer satisfaction and loyalty.
Q9: Are there any industry best practices for implementing EOQ?
Yes, there are several industry best practices for implementing Economic Order Quantity (EOQ), including:
- Regularly review and update EOQ calculations: Demand, holding costs, and ordering costs can change over time. Businesses should regularly review and update their EOQ calculations to ensure they are still optimal.
- Consider lead times and safety stock: Lead times are the time it takes to receive an order from a supplier. Safety stock is an extra amount of inventory kept on hand to buffer against unexpected fluctuations in demand or lead times.
- Utilize inventory management software: Inventory management software can automate EOQ calculations, track inventory levels, and provide real-time insights into inventory performance.
Q10: Can EOQ be used in conjunction with other inventory management models?
Yes, Economic Order Quantity (EOQ) can be used in conjunction with other inventory management models, such as:
- Safety stock models: Safety stock models determine the appropriate amount of safety stock to maintain based on factors such as demand variability and lead times.
- Reorder point systems: Reorder point systems determine when to place an order based on inventory levels and lead times.
Combining EOQ with other inventory management models can create a comprehensive inventory management strategy that is tailored to the specific needs of the business.
Conclusion
In conclusion, mastering the Economic Order Quantity formula is pivotal for businesses striving to enhance their inventory management strategies. By optimizing order quantities, balancing costs, and leveraging the EOQ model, businesses can achieve operational efficiency and financial success. Explore the integrated calculators to further refine your financial approach and ensure a holistic understanding of economic principles.
Useful calculators
To further enhance your financial knowledge, check out these calculators and resources:
- Weighted average cost of capital (WACC) formula calculator
- Debt-to-Equity ratio formula calculator
- Future value of an investment formula calculator
- Quick asset ratio (Acid-Test Ratio) formula calculator
By exploring these resources, you can broaden your understanding of various financial concepts and make more informed investment decisions.